高端成套装备自动焊接关键技术
煤机装备主要由大型结构件构成,其生产工艺多为格子间结构焊接,焊缝极多,工艺复杂,焊接质量要求高。由于结构的特殊性和焊接工艺的复杂性,目前以手工焊接为主,工人劳动强度大,无法保证焊接工作的稳定性和焊接质量的一致性,生产效率也无法进一步提高。
传统机器人自动焊接应用于煤机装备生产存在着工艺不适应、工件尺寸一致性差、空间焊达率低、智能传感技术和物流输送技术等极度匮乏等难题。为解决上述问题,部分大型煤机企业突破厚板多层多道智能焊接工艺、激光跟踪传感技术、格子间焊接变形自适应和大型复杂结构件焊接机械臂空间避障运动轨迹限制,实现了成套装备的自动化焊接,建成了煤机装备制造示范车间。其中最具代表性的是高端液压支架智能焊接车间项目与大型刮板输送机中部槽智能焊接生产线。
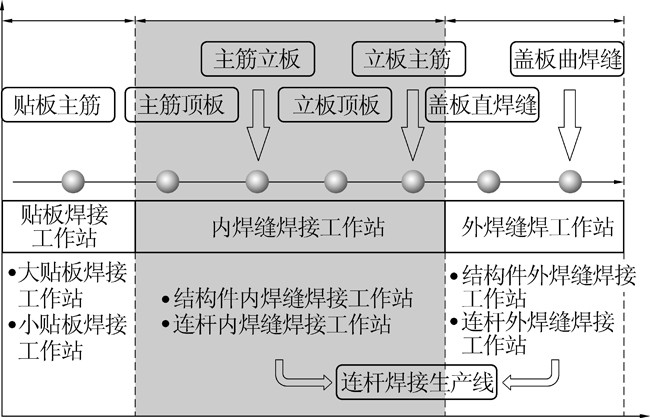
高端液压支架智能焊接车间机器人焊接工艺流程
适应煤机生产节拍柔性数字化车间
煤机装备需根据开采煤层要求设计基本结构进行生产,因此煤机装备生产是以订单为主导的生产模式,批量小,且涉及环节多,其生产要求制造离散化,工艺柔性化。针对煤机装备生产工艺,部分企业集成开发相关柔性制造系统,如“电液控阀芯柔性自动装配生产线”等。另外,在构建车间智能物流系统的基础上,应用分布式数控系统连接底层若干组柔性制造系统和单机数控设备,构建了数字化加工车间的一体化制造执行系统,实现整个车间的统一管理和数字化生产,从而提高生产质量与生产效率。
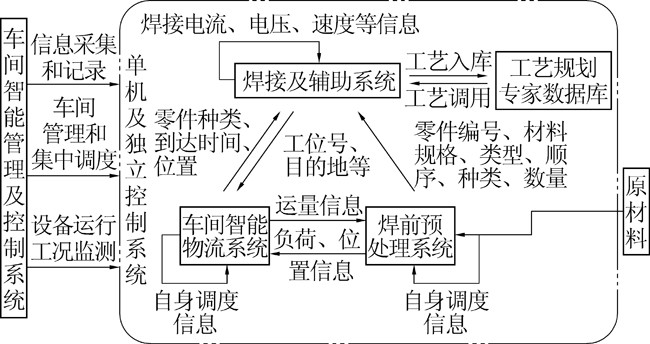
高端煤机装备制造示范车间组成及信息传递
关键智能制造技术
针对煤机装备的特殊应用环境,对其关键部件结构设计及制造重点研发突破,形成煤机装备核心制造技术。如创新提出了液压支架与围岩的强度耦合、刚度耦合、稳定性耦合原理及评价模型;发明大缸径能量耗散抗冲击立柱、三级协动护帮装置等新结构;提出大功率采煤机截齿齿体锥形面激光强化工艺和新的行走轮热处理工艺;研究Q890以上高强度材料焊接工艺;突破立柱激光熔覆、修复热处理、再制造毛坯快速成型等再制造关键技术。在上述智能制造技术突破的基础上,煤机装备智能制造产业初见成效。
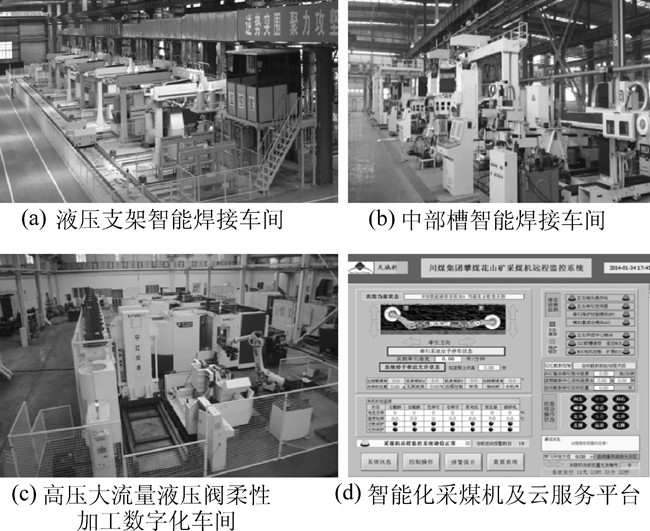
高端煤机装备智能制造示范
参考文献:《德国工业4.0与中国煤机装备智能制造的发展》